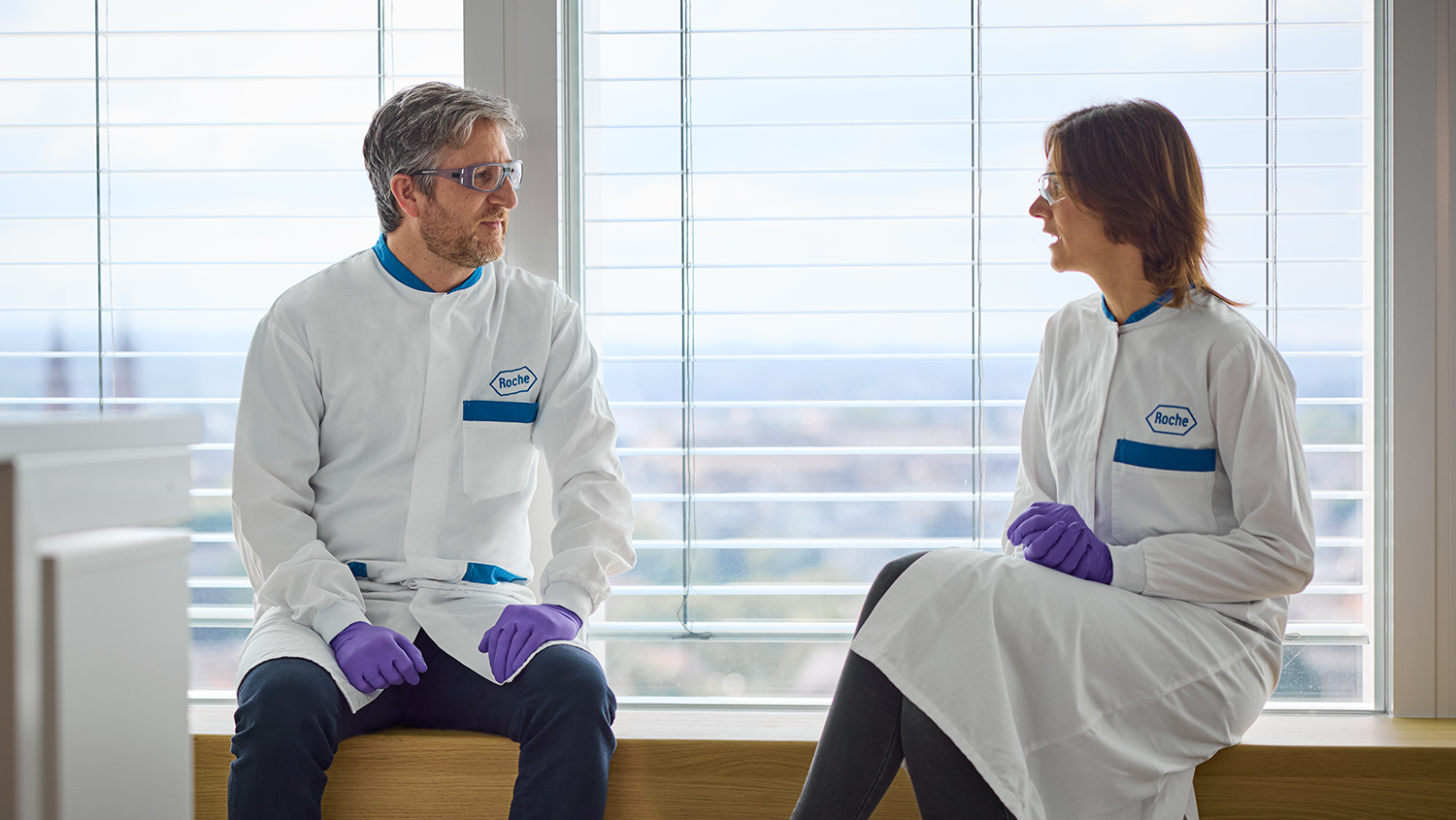
Interiors for Labs
Enhancing employee experience in labs
In science, the environment youRosalind Franklin - Biochemist
create for discovery is as crucial
as the questions you ask.
Enhancing employee experience in labs
Achieving a cohesive, holistic workplace including technical and non-technical spaces is a target for all of our spaces. The whole workplace should be visually connected so that it is inclusive, supports the community and a culture of collaboration. Clear, functional, elegant, open and transparent, related to the local context, showcasing new technologies, and the focus on people’s well-being and sustainability are also essential to Roche’s approach to the design of our laboratories.
These design principles apply to General Biology, General Chemistry, Instrumentation and small-scale production labs and beyond, wherever applicable, and are focused on the impact of key interior design elements. They should be read in conjunction with the specific laboratory technical requirements, which will differ depending on the laboratory type.
The workplace includes laboratories, technical support zones and related office space, with areas for write-up, collaboration, focus work and recreation. These spaces should be connected through both visual openness and cohesive design element – materials, colours and details to create a unified experience. Laboratory space planning is driven by adaptability, functionality, health and safety and the comfort of users.
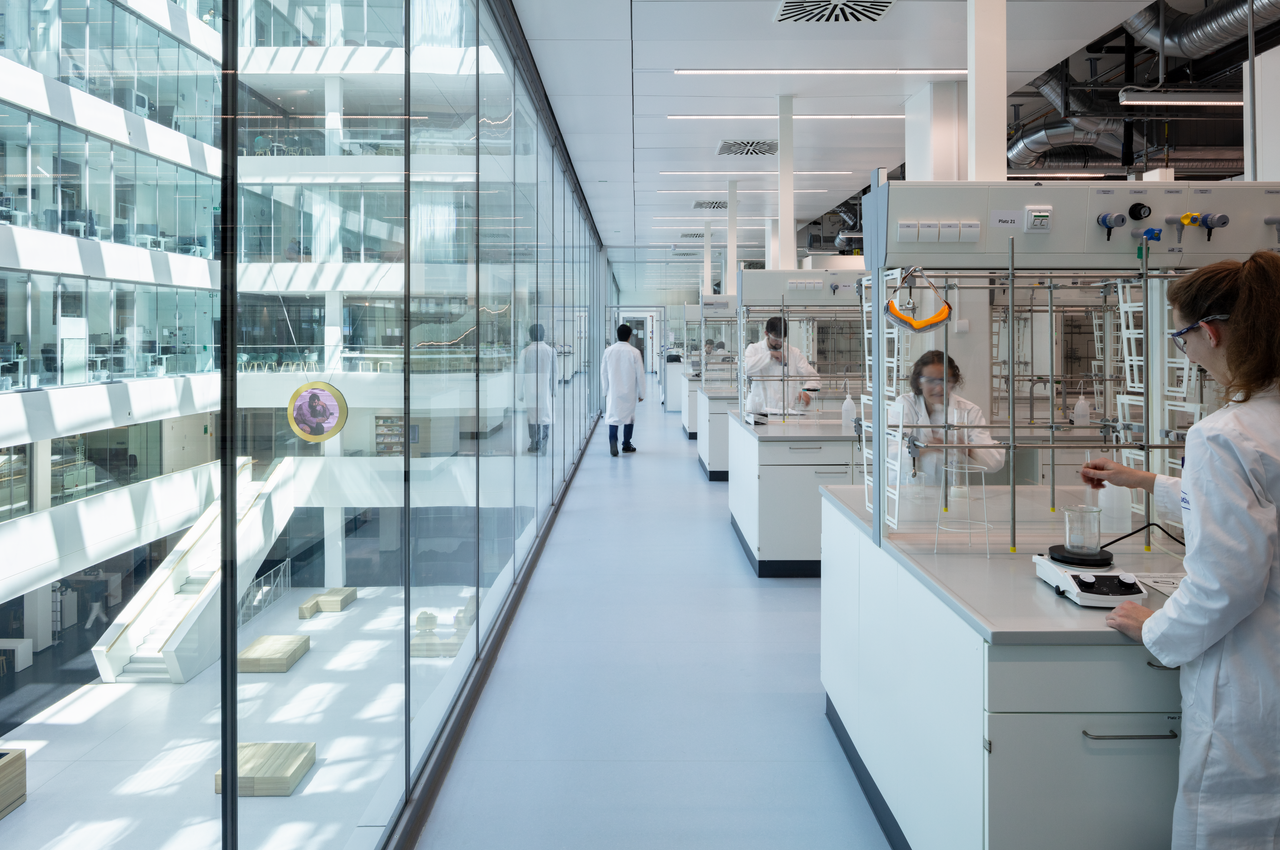
Laboratory planning grid and lab module
Most scientific work in the lab relies on tests and experiments on free-standing or benchtop equipment, preparing samples at the workbench and moving samples, material and reagents between equipment and lab benches.
To ensure this work can be performed efficiently, laboratory layouts shall follow a continuous structural grid and adopt a modular and systematic integration of utilities, partitions and lab casework. The unit consisting of a structural bay, its associated utilities infrastructure and case work is referred to as a lab module.
The individual lab module is determined by the science activities and the resulting necessary infrastructure requirements, taking into account the various technical disciplines as well as the interfaces with other modules and the building.
Adaptable laboratory workplaces
To meet rapid changes in science while also meeting cost targets, the design of lab facilities must include a concept for adaptability.
The key to achieving a high degree of adaptability is the following:
- Design the lab modules with a generic approach and based on the size and complexity of the project, consider reducing the amount of different modules to the minimum.
- A regular grid structure allowing large contiguous areas (and not a room structure).
- Define the bandwidth within which changes are possible, based on current and future functions: this may include extending the laboratory zone into the office zone or vice-versa, and adapting the utilities.
- Determine acceptable durations for implementation of changes, depending on how much shutdown is acceptable for business operations.
- Identify what is needed on day one and what can be enabled, but not installed, for the future (day two).
- The provision of utilities should be planned in a scalable manner to minimise the installation of surplus systems and allow for a gradual expansion as demand increases.
- Conceptually separate the primary and the secondary technical installations. The primary installations include main HVAC, water, gas, electricity lines and should be planned independently of the users. The secondary installations include the links between the main lines and the point of use. These are driven by the user’s needs and should be easily adaptable.
Utilities distribution
To enable a high degree of flexibility for reconfiguring benches and equipment, supply connection points should be easily accessible with minimal effort and horizontal utilities distribution should be routed through the ceiling. Various drop-down systems are available to deliver utilities to the point of use, each offering specific ways to support adaptability in the laboratory.
Generally, there are four different concepts of bringing the utilities to the point of use: ceiling service panel with free-hanging utility lines, media columns, media wings and media spines. Each concept has its benefits and disadvantages, and needs to be evaluated depending on science needs, costs, maintenance, safety, transparency and desired aesthetics. All four concepts can achieve a cohesive, holistic workplace experience.
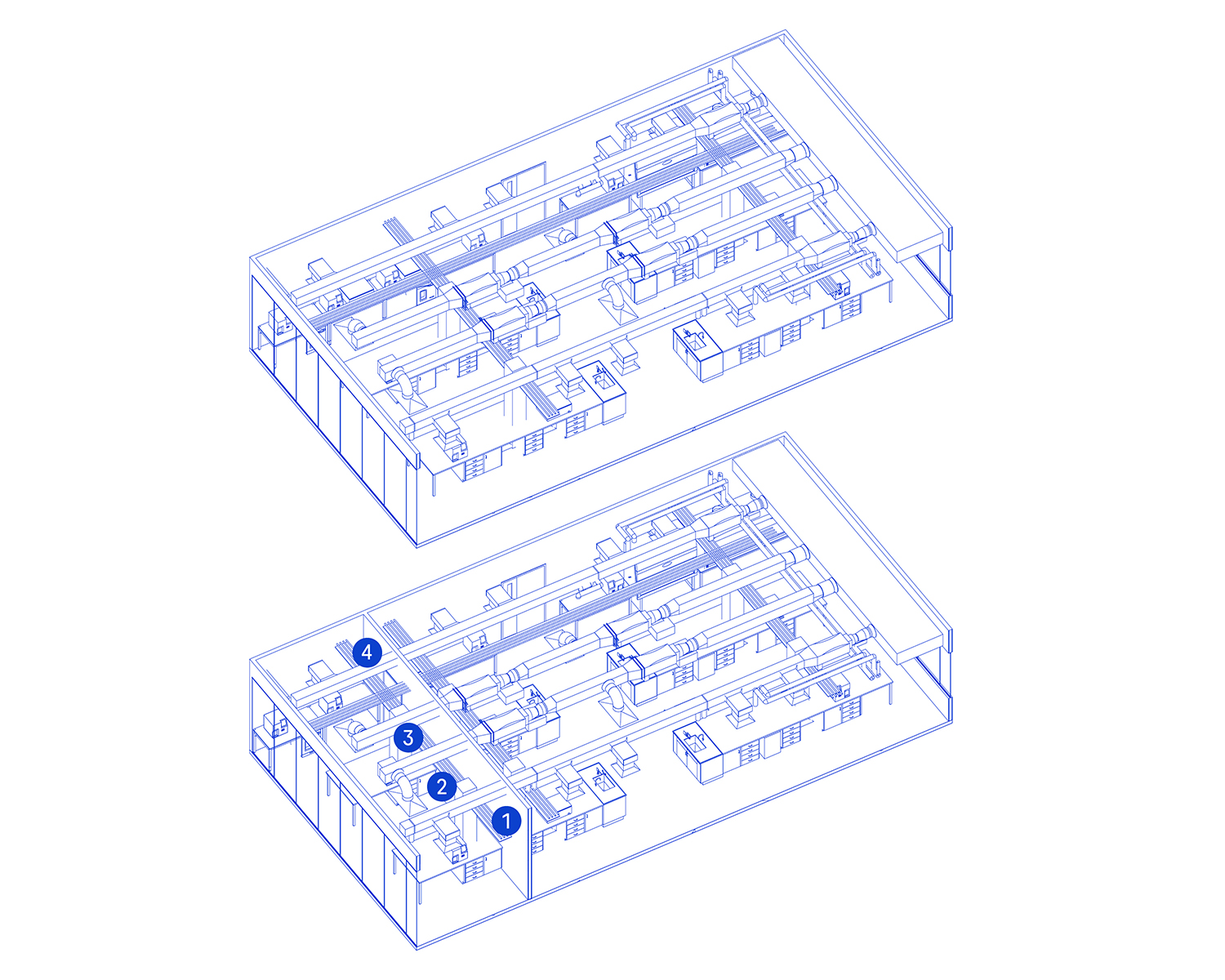
Access to daylight and views
All workspace areas should provide natural light and views to the outside for users’ well-being. This is no exception for the technical workspace (labs), ideally positioned along an exterior wall. If labs need to be interior, for example for very sensitive equipment, this should be based on specific use and never be a permanently assigned working space. Generally, labs need a deep footprint for efficiency in the use of the space. This must be balanced with the need of daylight and considered when designing the facade. When possible, avoid placing labs on south-west facades to reduce solar gain and cooling demands; north and north-east exposures are preferable.
Effective space planning involves strategic placement of utilities and casework, whether parallel or perpendicular, to maximise natural light penetration and enhance visual transparency between adjacent areas.
- Main circulation should be positioned as far as possible from the exterior walls/windows to maximise daylight in the working lab area.
- Consider glare protection, interior solar screens with 1-1.5% openness can filter light effectively while minimizing glare. In special cases a black out layer may be required for full lighting control.
- To protect from the sun, exterior shading is highly recommended. If this is not possible, consider applying a film to the exterior side of the glass.
- Compensate for the lack of greenery inside labs by positioning plants in adjacent locations – such as office spaces – visible through the lab windows, if this is permitted, or providing outside views.
- Learn more about Bright spaces
Transparency and visual connection
Display of innovation and science is a key objective of our workspaces, featuring the central function of research and development to achieve the Roche purpose. Visibility and connection between technical and non-technical workspaces is essential, ideally achieved through a single transparent surface to foster visual connectivity and a sense of openness. Module orientation should also support smooth flow and sightlines. Special care should be taken with the detailing of glazed partitions to maximise transparency and elegance by minimising frames, ensuring large panel modules. Refer to corporate signage for safety manifestations on glass.
Consider data protection if outside space is accessible for non-authorised persons.
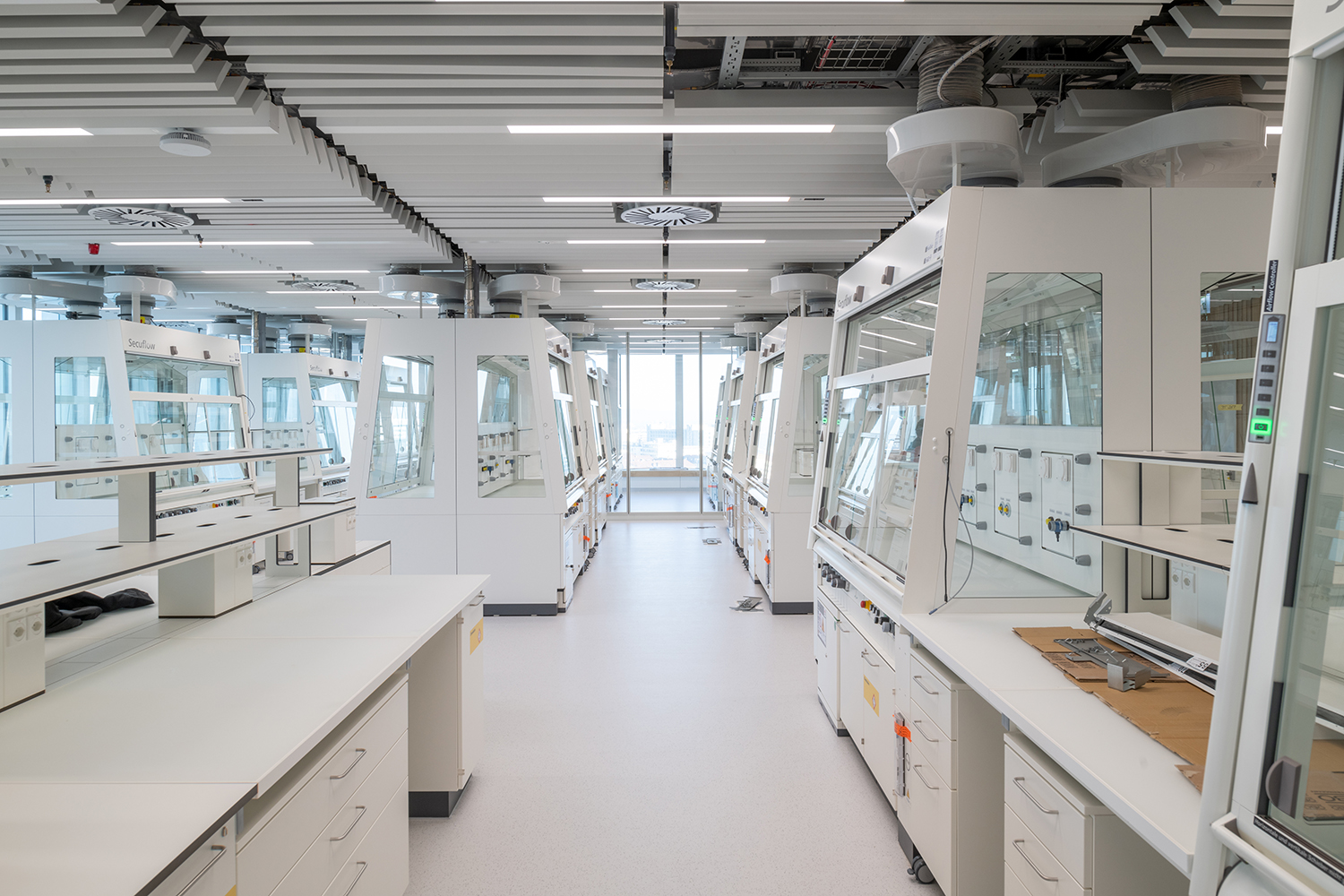
Clear, safe and purposeful circulation
Allowing for a clear path allows for seamless flow and also contributes to safety and intuitive way finding.
- Design the corridors with a view or transparency into another space at the end, avoiding opaque walls as end perspective.
- Avoid redundancy of corridors.
- Long corridors should be broken up by other space types to encourage functional active use of the space, when possible.
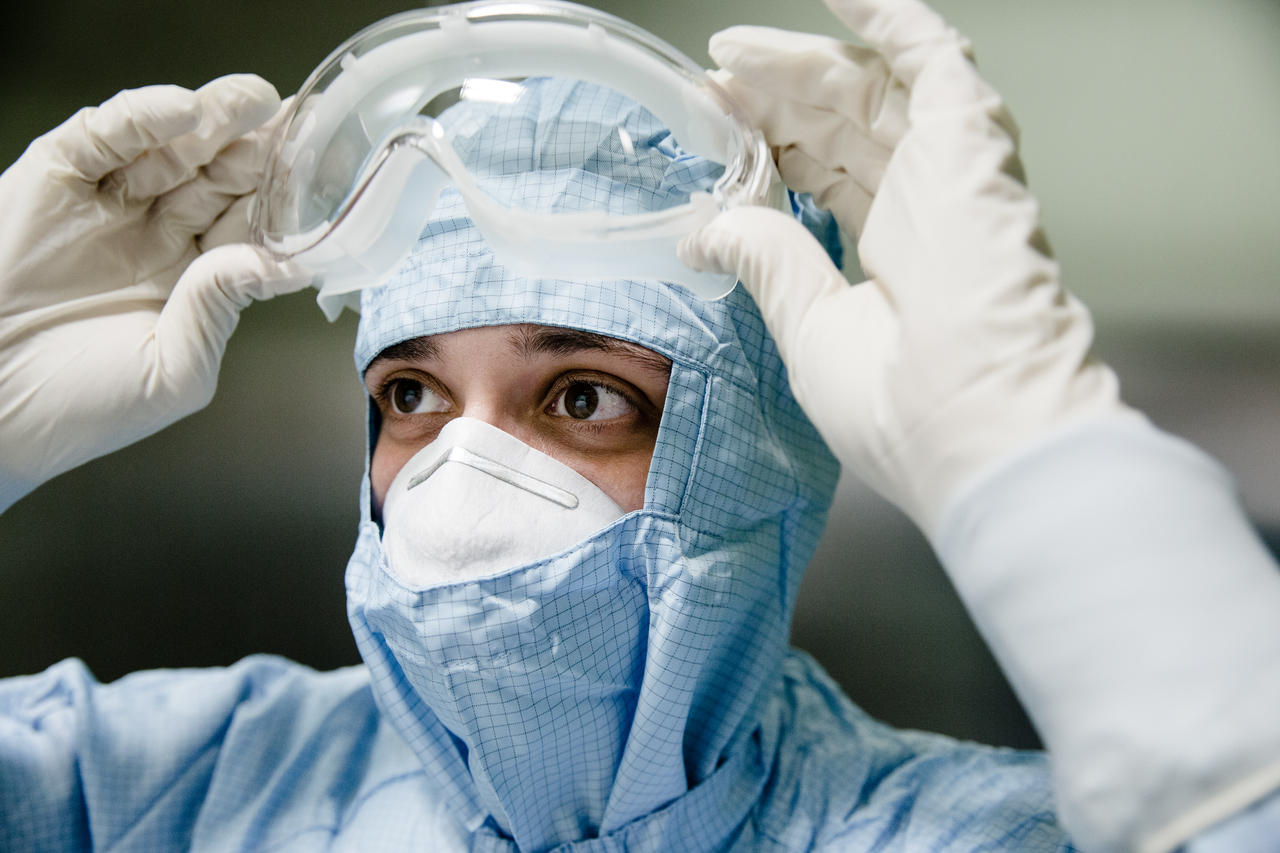
Gowning/degowning rooms
Gowning rooms are dependent on the containment and safety protocols, and as such they are an integral part of the daily experience. Gowning rooms shall be sufficiently sized to comfortably put on personal protective equipment and provide storage space for street clothes, shoes and personal belongings.
The different steps involved in putting on the Personal Protective Equipment (PPE) shall be designed in such a way that it becomes intuitively clear what the sequence is. As a transition zone between non-laboratory and laboratory areas, we recommend establishing some transparency to both spatial zones in order to facilitate orientation and prepare for the next space.

Storage space
Lab facilities require substantial storage space for consumables, samples, reagents, and other materials. To prevent core lab areas from becoming overburdened with storage, it is essential to prioritize central storage solutions, potentially augmented with a digital automated inventory management system. Storage space in the labs should be limited to the materials needed for one or a few days.
The right materials for labs
The finishes of the labs must follow a clear interior design materiality concept. It is important to consider that materiality and atmosphere have an influence in the perception and well-being of the people working in the lab. For example, creating a warmer environment by introducing wood or alternative warm materials when possible, or even through transparency into an adjacent space.
The finishes must be chosen taking into account several technical considerations, including hygiene requirements (depending on the type of lab), health and safety, life cycle (cradle-to-cradle) and sustainability criteria. In order to support material choices, refer to Roche laboratory Performance Specifications and Roche Laboratory Materials Catalogue to identify appropriate finishes for each lab type.
Easy maintenance
- Aim to keep maintenance requirements at a minimum, by selecting materials that are durable and easy to clean and maintain.
- Horizontal surfaces and flooring should be smooth, as textured finishes are harder to maintain. Minimise joints and seams wherever possible.
- Avoid graphic or directional patterns, they should only be introduced when naturally occurring in the material, such as the organic grain in wood or exceptionally in flooring as homogenous small-scale patterns.
- All furniture must be sturdy, with wipeable surfaces rather than fabric.
- All work surfaces (e.g. bench tops and counters) must be impervious and resistant to chemical solvents (e.g. formaldehyde, phenol, and ethanol and disinfectants). The bench tops shall be free from stains and must be seamless.
Light and neutral, with accent colour contrast
A consistent colour scheme derived from the building materiality concept should provide a continuity between the technical workspace and the non-technical spaces for consistency and to strengthen the identity of the overall workspace. The palette should be predominately light, warm and neutral (white or soft greys). Lighter shades enhance the sense of spaciousness, making spaces feel larger and more open. Sixty percent reflectivity or more is recommended.
Adding contrast is also important for character, visual interest and space clarity. Make sure there is at least one surface which brings a contrasting material colour to balance the perception of the space. Without being too dark, this could be the flooring, a wall within the lab or a surface outside, but visible through the transparent glazed partitions. Darker finishes should be minimized.
Incorporate an accent colour to create a welcoming laboratory space, which feels integrated as part of the entire workplace, and consider:
- Avoid demarcating the circulation areas within the labs with different colours, the flooring should be homogenous.
- Potential trip hazards, emergency safety equipment and eyewashes, typically required in bright colours by local jurisdiction, need to be thoughtfully integrated into the interior design and not appear as an afterthought.
- Furniture can be used to provide complementary accent colour within the space, but not the casework.
- All casework should be monochrome standard white colour, unless there is a specific different technical requirement.
Learn more about Inspiring colours
Technology experience
As technology is increasingly integral to lab operations, designing to accommodate it effectively in the workspace is essential.
Technology in the lab environment refers among other things to laboratory equipment, digitalisation, automation and robotics. In this guide, we only focus on the components that interface with interior design decisions.
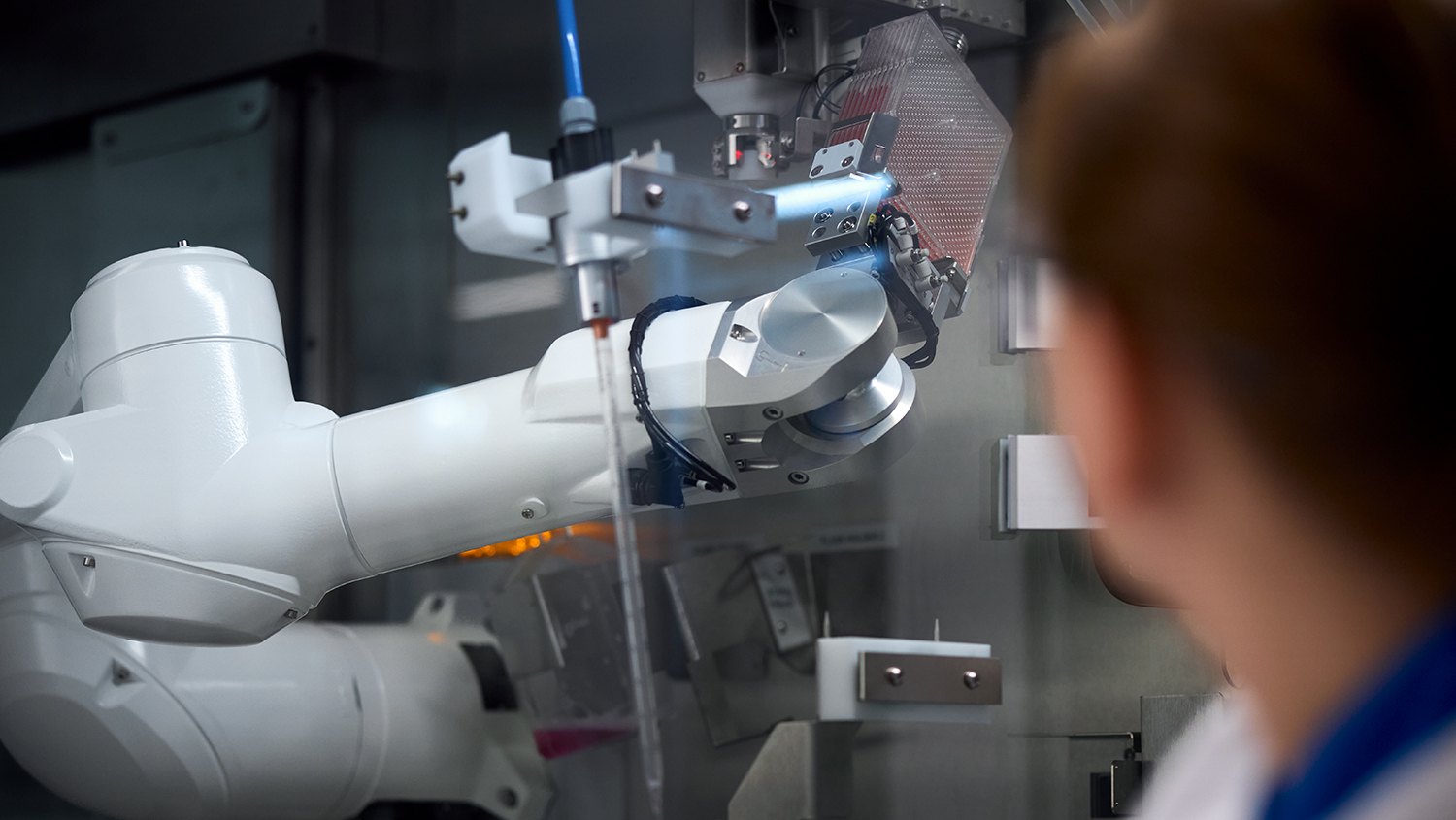
Robotics, the lab of the future
As more and more lab operations will become automated and carried out by robot technology, it is important to address this evolution in the design.
Designing labs for robotic automation requires careful consideration depending on the type of building and robotic equipment as well as the degree of automation.
Existing buildings may need creative retrofits to address limitations such as slab-to-slab height or structural load, while new buildings can integrate automation-ready features from the initial design. Hybrid labs combine human and robotic workflows, whereas fully automated labs emphasise end-to-end robotic operations, requiring different infrastructure and safety measures. Self-contained robotic units are static and relatively compact whereas mobile robots require ample open space for circulation.
Structure
- Due to the addition of heavy robotic equipment and related infrastructure, the building should be able to handle increased structural loads, both static and dynamic.
- In order to ensure seamless robot navigation, the floors should maintain flat thresholds between laboratories. In the case of existing buildings, consider raised floors or self-leveling equipment to accommodate robot integration without disrupting structural integrity.
Layout
- Lab spaces should adopt a modular layout with centrally located lab islands while ensuring that utilities are easily reconfigurable to support future scalable automation. This will allow robotic equipment to be easily rearranged as scientific methods and tools continue to evolve.
- Pathways should be designed for unimpeded movement of robots and personnel. Ensure aisle and hallway widths are sufficiently large to allow for smooth navigation.
Fitout
- Labs should be designed with an open ceiling to enable flexible and reconfigurable utility connections.
- Doors should be automated with self-opening mechanisms, incorporating robust sensors and control systems to support mobile robot operations. Equip existing building systems, such as elevators and doors, with digital interfaces to enable seamless communication with robots.
- Incorporate only movable lab furniture and ensure it includes floor profile strips (VL markers) for easy scanning by mobile robots.
- Install movable utilities distribution, such as movable media columns.
- Balance the specific needs of humans and robots, which in some instances may be competing: pay attention to some materials (such as glass) that may interfere with robots’ sensors.
- Include blackout blinds, since direct sunlight may interfere with robots’ sensors.
Key to Labs interior design
- Consider laboratories interior design as part of the entire workplace experience.
- Design structural grid and vertical shafts to enable clear and efficient circulation while maximising large, uninterrupted spaces.
- Adaptability is essential for zoning and lab modules: consider the level of pre-instalment required for infrastructure.
- Leverage daylight, creating transparencies and visual connections for a bright and open lab space.
- Ceilings should form a clearly structured harmonious datum, integrate installations, lighting and acoustic solutions.
- Use bright and neutral materiality, ensuring one contrast surface and/or one accent colour, bringing clarity and vibrancy.
- Enable smart building and equipment technology, incorporate adequate space for networking, communication devices and sensors.
- Define the level of technology and robotics integration at the project onset to ensure that all design requirements are captured.